Advanced-Framed Walls Bring Efficiency to Illinois Home
As homeowners are becoming more concerned with energy efficiency and energy codes have become more stringent, many builders are looking for ways to improve the energy efficiency and environmental footprint of their homes.
One of the most cost-effective ways to improve energy efficiency while maintaining structural integrity is through advanced framing, a system of construction framing techniques that maximize material usage while providing more space for cavity insulation versus conventional framing.
Conventional framing of the past typically did not make efficient use of wall framing materials and often resulted in cavities or voids that could not be insulated. Advanced framing reduces unnecessary structural members by placing framing members only where they’re needed. In addition, by maximizing space for cavity insulation and minimizing the potential for insulation voids, advanced framing delivers significant energy performance and cost savings for the homeowner and can help builders meet the requirements necessary to earn the Energy Star label for new homes.
Advanced framing techniques took center stage recently at the “Inside View” demonstration house in Lockport, Illinois. Builder Beechen & Dill incorporated many of the practices into a new home in its Creekside Estates development, then opened the house up for tours so that other building pros could learn about the techniques themselves in a true-to-life setting.
For the Inside View house, sponsored by APA – The Engineered Wood Association and the USDA Forest Service, Forest Products Laboratory, Beechen & Dill employed a number of advanced framing techniques for the walls, including:
-
2x6 studs spaced 24-inches on center
Conventional framing typically consists of 2x4 or 2x6 wood framing spaced 16 inches on center. Advanced framing methods increase 2x6 stud spacing to 24 inches on center. This stud spacing works well with all commonly used sheathing and insulation materials. Because OSB and plywood sheathing is a nailbase, 24-inch stud spacing also works well for almost any siding material, including some vinyl products that require closer fastener spacing. For builders striving to meet the requirements of the International Energy Conservation Code, 2x6s spaced 24 inches on center makes it easier to meet the energy code requirements for R-20 wall insulation with lower-cost R-19 batts.
-
Ladder blocking
Advanced framing ladder blocking is used at wall intersections and at two-stud corners, and is typically horizontal 2x lumber spaced at 24-inches on-center. Ladder blocking provides a cavity that can be easily insulated, while the old three-stud interior wall intersections and corners were nearly impossible to insulate.
-
Insulated three-stud corners/California corners
Insulated three-stud corners also eliminate the isolated cavity produced by the old corner framing methods and are one of the most popular insulated corners used by builders that incorporate advanced framing.
-
Insulated single-ply and double-ply engineered wood headers
Advanced framing headers offer increased energy efficiency by replacing framing materials with space for cavity insulation inside the header. Advanced framing headers are sized for the loads they carry, which is why engineered wood headers such as laminated veneer lumber (LVL) and other types of structural composite lumber (SCL) can optimize the amount of space for insulation above larger openings and on first floor walls that transfer heavier loads.
Along with these wall techniques, the home includes a robust and more efficient floor system that more easily accommodates ductwork in conditioned space. Look for more on those details on this blog later this month.
Following the tours, the Inside View house will be finished and sold just like any other home. Future occupants won’t notice the techniques—the two-story home looks no different than its future neighbors, with a brick façade, trim accents, a two-story great room, and three-car garage. The Home Energy Rating System (HERS) index decreased by 1.5 points on this home, a difference homeowners will notice in the form of lower energy bills.
For Beechen & Dill, it’s one more step in a company-wide effort to build efficiently and more practically. “We’re always striving to be on the cutting edge. We were the first in the area to build energy-efficient homes and to guarantee energy bills,” says Ed Kubiak, director of construction. “With prices going up and labor harder to find, techniques such as these that reduce energy use while making more efficient use of materials and allowing for more efficient construction are the direction the industry needs to be going.”
About the Author
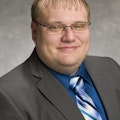