As home builders take more creative approaches to new-home construction to bypass labor shortages and supply chain roadblocks, Brian Gaudio, CEO of Module Housing, in Pittsburgh, says modular construction is the most logical way forward. But a lack of research and proper worker training, he points out, slows advancement of off-site construction methods when left in the hands of inexperienced builders. That’s why Gaudio started the Last Mile Lab, a Pittsburgh-based construction testing facility that includes vocational training to bring more diversity to the construction workforce—a model Gaudio is looking to replicate in other communities across the nation.
PRO BUILDER: When was the Last Mile Lab launched and what motivated its creation?
Brian Gaudio: The Last Mile Lab was created in early 2022, and the impetus for it was twofold. First was the lab. We’d asked our factory partners to push the envelope in terms of energy performance with more advanced construction materials than those currently on the market. We believe these systems are going to create a better product in the end, but manufacturers are busy, and they don’t necessarily have time to be doing research and development.
Our 15,000-square-foot space in Pittsburgh allows us to work with some of those building product manufacturers, as well as the National Renewable Energy Laboratory and Carnegie Mellon University, to develop applied solutions that can help push the modular industry forward. We’re testing new product applications we think could be best practices, creating case studies around those experiments, and then sharing the results with the industry.
PB: What educational resources are offered?
BG: Education and workforce development comprise the second component of the Last Mile Lab. Modular construction is very different from traditional building, and we wanted to create a labor force specifically trained for it. We partnered with the Trade Institute of Pittsburgh to offer vocational resources for students.
The Trade Institute is a nonprofit construction workforce training organization in Pittsburgh that serves populations with barriers to employment; a significant percentage of its student population has been previously incarcerated. We’re working with the Institute on new workforce development programs specific to modular.
RELATED
- Building Talent Foundation’s Plan to Build and Retain a Talented Workforce
- Vaughan Buckley on Restarting a Former Katerra Factory
- Attracting Talent in Today’s Skilled Labor Market: 84 Lumber's Maggie Hardy Knox
Our first cohort of students participated in field trips to both a modular factory and to recently completed Module homes. This year, we have an exciting new project coming up for them: an ADU [accessory dwelling unit] that will be on display in Washington, D.C., this summer. It’s a great opportunity for the program’s graduates to work on a real project to gain experience.
PB: Why, specifically, did you partner with the Trade Institute of Pittsburgh, and how can this kind of training program benefit the construction workforce as a whole?
BG: The Trade Institute has an open-door policy, [unlike some] other apprenticeship programs that may require a driver’s license, a math test, a negative drug test, and other prerequisites.
The Institute’s program is open to anybody who wants to get into construction, and that’s really important for the construction industry right now. If we create opportunities to bring more diversity into the workforce, it will benefit everyone.
PB: How has it benefited the Pittsburgh area and how can it be replicated elsewhere?
BG: We’ve completed roughly a dozen projects, and most of those are in Pittsburgh. We’re now looking at the Mid-Atlantic and the Midwest.
The Last Mile Lab functions almost like a finishing facility, if you will. It’s not a full-fledged factory, but it’s a way for a city or an area to test the waters of modular. We’re partnering with Enterprise Community Partners, a national nonprofit affordable housing organization. They have a development arm, which is the largest Black-led affordable housing developer in the country.
We’re partnering with Enterprise on a feasibility study to look at how what we’re doing in Pittsburgh might be replicated in other urban communities, and we’re kicking that work off [this month].
Modular construction starts are outpacing traditional housing starts, not in terms of volume, but in terms of growth rates. As the labor shortage gets worse, modular makes more sense, but its expansion begins with research and education.
About the Author
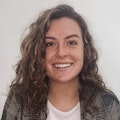
Layne Deakins
Layne Deakins is the associate editor for Pro Builder, PRODUCTS, and Custom Builder. She writes feature articles, contributes HorizonTV videos, manages social media accounts, and produces e-newsletters for all three brands. Layne is a 2021 graduate of Pennsylvania State University.