Modular Builders Mobilize to Deliver Prefab Modules for Coronavirus Care
As the shortage of critical medical equipment threatens caregivers and their ability to treat people with COVID-19, modular home builder Volumetric Building Companies (VBC), in Philadelphia, has assembled a coalition of at least 20 off-site manufacturers to build and deliver prefabricated modules that can provide more than 1,500 patient beds per week. Ramping up production could take as little as three weeks, pending an official order from the U.S. Army Corps of Engineers.
Vaughan Buckley, president of VBC, also approached the Federal Emergency Management Agency (FEMA), the Department of Housing and Urban Development (HUD), and the Veterans Administration (VA) with this high-volume production initiative to increase the availability of patient beds with Supplemental Medical Care Units, or SCUs. The concept is more in line with the Army Corps’ mission to increase the nation’s capacity to fight the coronavirus, and is among the options being evaluated.
“We need the government on board so we can ensure we would have the supply chain necessary,” Buckley says. “We wouldn’t want a coalition of 40 to 50 factories to produce just 100, 200, or 1,000 of these modules. The Army Corps of Engineers is asking us how many tens of thousands we can give them.”
SCUs are high-end modules compared with the plywood FEMA trailers used to shelter people displaced by hurricanes or other natural disasters. The rectangular modules accommodate three to five bedrooms and two bathrooms, and can safely quarantine patients while providing a secure healthcare environment. They also are built to a universal standard and can be placed in parking lots or open fields and connected together to form a series of one-level modules or stacked up to three stories. SCUs are not meant for critical patients but do allow non-critical patients to be cared for by healthcare professionals off-site, freeing up limited and crucial hospital space.
The modules are expected to cost about $18,000 per patient room compared with about $65,000 to $70,000 for FEMA trailers.
Buckley and his team of architects began brainstorming for a possible solution as professional and college sports leagues postponed or cancelled their seasons in the first week or so of March. He sought advice from mentors with experience building healthcare facilities and found there was little overlap between the building and design codes from the Facilities Guideline Institute (FGI) and the Army Corps of Engineers. Other modular builders he consulted also wanted to do something to alleviate the crush on hospital space caused by COVID-19 cases, but didn’t know how.
“This is a really a good opportunity to synthesize the industry in a way we could all move together, because if we don’t, we would have 30 to 40 different entrepreneurial factories that want to help and go out there to make their own plan.” say Buckley. If that was the case, “We would have an inconsistent solution to the crisis,” he says, likening it to the tens of thousands of trailers meant for displaced victims of Hurricane Katrina that went unused or were disposed of or auctioned.
After two weeks of around-the-clock effort, VBC created a design that meets the FGI, the International Building Code, and Army Corps of Engineer guidelines for healthcare facilities. Each module was designed to fit transportation regulations for flatbed truck cargo under 14 feet wide, allowing it to travel without an escort or special permit in most states.
Within weeks of the initial idea, 20 other modular builders had signed on. Each manufacturer will use VBC plans and specifications to build modules and also integrate the bathroom pods sourced from VBC’s North Carolina facility. Making and sending fellow manufacturers the bath pods, which have a concrete base and impervious surfaces, non-combustible steel framing, and consistent plumbing and electrical runs, will remove complexity in the coalition’s supply chain.
“We weren’t creating a design so we could build it. We were creating a design so everyone can build it,” says Buckley. “Our whole industry has come together in a way I haven’t seen before. Everybody wants to do the right thing.”
And because most offsite manufacturers are located in areas with relatively few cases of COVID-19, production is expected to be reliable and the labor force less at risk of exposure.
Buckley estimates each coalition partner could produce modules for at least 100 patient beds per week, and more manufacturers (perhaps up to 50), could join the effort if the Army Corps of Engineers orders the SCUs, with the federal government (probably through a General Service Administration broker) contracting directly with each manufacturer.
Unlike FEMA trailers, SCUs are designed for durability. When the pandemic passes, Buckley foresees these modules being stockpiled and eventually used by municipal housing authorities or private agencies to provide affordable housing for veterans, seniors, and homeless people. Modules can be stacked and draped with a facade, or used as a low-cost solution by plugging in one or two units into a multifamily building.
In the meantime, Buckley is standing by for a call from the Army.
About the Author
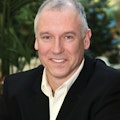
Mike Beirne
Mike is the senior editor of Pro Builder and Custom Builder magazines. A two-time Jesse H. Neal Award winner, Mike has nearly 30 years of journalism experience plus numerous news and feature writing awards, including honors from the Society of Professional Journalists, the American Society of Business Press Editors, and the National Association of Real Estate Editors. He also operated a masonry restoration business for more than two decades. [email protected]