Five years of Lean implementation projects with more than 1,500 suppliers and trade contractors has yielded more than 10,000 cost-saving ideas without asking for bid-price reductions. Over time, patterns emerge where we see the same issues in virtually every location. Many are obvious and frequently elicit a “How did we ever miss that?” response. Some are subtle, while others are quite complex, involving significant changes to the building process, modifications to the plan design, or major reforms to a building company’s management practices.
20 Cost-Saving Ideas for Home Builders
Here are 20 ideas listed by supplier/trade in general build sequence that will produce bottom-line dollars in short order — mostly in the “obvious” category. It’s rare that a builder does not find opportunity in at least half of these, as long as they open their mind and eyes and listen to the folks who spend all day, every day, building their houses. The biggest obstacles are momentum, ego, and fear. Letting go of “we’ve always done it this way” is step one. Step two: Accept the fact that even though you’ve spent the past five years trying to determine how to build for less, you don’t know everything. Finally, quit worrying about the boss asking why you did not find this stuff before and push on. You’ve been extremely busy and short-staffed the past five years. Besides, when the money flows in, this issue will be quickly forgotten.
1. Foundation concrete. Check and verify all wall sizes, footer sizes, and concrete PSI requirements. It’s not unusual to see 16-inch footers where code requires 12 inches, or poured walls at 10 inches where 8 inches are required. Concrete is also commonly over-specified, using 3,500 or 4,000 PSI concrete where 3,000 will work just as well. Savings of $350 per unit are common.
2. Foundation labor. Each unnecessary corner costs at least $25 for a slab, $50 for a crawl, and $100 for a basement for labor and material. If you design out of the plan a setback/jog that runs all the way up to the roof — thus eliminating the extra wood, siding, insulation, drywall, paint, fascia, soffit, and labor it requires — count on another $75 in savings per corner for a single-story and $125 for a two-story. Add this up and getting rid of a setback that can be treated just as well with design elements can save $450 per unit.
3. Framing labor and material. The amount of money and time wasted in oversized and unnecessary headers, overbuilt corners, and excess kings, jacks, and cripples is a national epidemic, often adding up to more than $500 per unit ($1,000 is not unusual). In areas where roofs are stick-built, double the numbers. It may be a challenge to get your framer to change and your local inspector to follow the state code, but the stakes are too high to not make a dedicated effort here. We have yet to find a builder that seriously tackles this issue and finds anything less than substantial return.
4. Engineered wood products. Thorough analysis of almost any house by an engineer who truly understands that his job is to help you get your plans approved at the lowest cost will yield significant savings in TJIs, web trusses, and lam-beams. Codes are set at 250 percent of the calculated load requirement. Does it really make the house better to have support structure that carries 400 percent? Most of this waste is unintentional — no one has taken the time to do thorough calculations and most use a lot of assumptions in their takeoffs that are wrong. Not just any engineer will do. Find one who “gets it” and hundreds of dollars per unit will accrue.
5. Truss/roof systems. This issue is identical to engineered wood products, where detailed examination and calculation nearly always yields savings, with an important addition — roof pitch. Time and again, we have seen builders resist a reduction in roof pitch due to “market concerns,” then proclaim they love a new design based on the original and can’t wait to build and sell it. Only later do they discover that the roof pitch of the new design has been reduced at a significant cost savings. However, it’s not as simple as reducing the pitch. It’s about getting the elevation details right, and a good architect is a must.
6. Roofing. It’s amazing how common it is to find two or three square (six or nine bundles) of shingles left over on job sites, yet everyone always seems surprised. At around $100/square, you are lucky if the restocking charge only costs you $50, but more often than not, the material just disappears. Whether it walks off the job, ends up in the dumpster, or is just not being credited back by the supplier, there is no excuse for having more than a bundle or two of shingles left over, and those should be left with the homeowner for potential future repairs. This requires detailed, accurate takeoffs that are thoroughly reviewed and adjusted after the first model is built.
7. HVAC. Many builders don’t realize that it can be just as bad to oversize a compressor unit as to undersize it. As builders implement energy-saving features such as improved insulation of walls, ceilings, and foundations, better house wraps, and roof sheathing, both heating and cooling load drop significantly. There is software available to do the calculations you need. Placement of the air handler inside the structure and reducing the length of line-sets to the compressor also increase efficiency. Get all of this right and it’s common to drop a half or even a full ton of capacity, saving $200 to $500.
8. Plumbing. Sit down with your plumbers and go through a couple of plans in detail. You’ll find it’s rare that all drain locations, feeds, sumps, stacks, and plumb walls are precisely identified on the plans with exact locations. Every single missing measurement means more work, more time, and a greater chance for errors, omissions, and rework. This might range from $100 in buried time to $1,000 to bust out a floor drain and move it. The time spent up front to get this right is a pure investment, never an expense.
9. Electrical. Similar to plumbing, it is unusual to find all the details laid out on an electrical plan for switches, outlets, 220V lines, smoke detectors, fan-light combinations, 3-ways, 4-ways, etc. Not having these takes time and causes rework. A simple way to save $100 or more per unit is planning ahead to locate electrical panels close to the service entrance.
10. Insulation. This sounds deceptively simple, but the best way to save on insulation is to jump back up to No. 3 and get your framing straightened out. Any installer can tell you that some houses are much faster and easier to work in than others, taking far less cutting, piecing, and stuffing, and that can usually be traced back to the framer. Time is money. When your structure is festooned with excess headers, kings, jacks, and cripples, and your corners are needlessly complex, insulating is much more difficult, not to mention less efficient. Have you ever walked houses with your framers and your insulation installers together? I’ll bet not. Take this seriously and save your insulation company so much time that in six months they’ll be willing to reflect it in their next bid.
11. Drywall. Have you ever looked in the dumpsters, marveling at the quantity of drywall that you paid for, shipped to your site, then pay again to haul it away and bury it? Your immediate assumption is that the drywall hangers were sloppy, and that could be the case. But perhaps it is really a design issue. See those 8-foot, 3-inch walls in the garage? See the 12-foot, 2-inch bedroom lengths? Or perhaps the purchasing manager got a great deal on 4x12-foot sheets. Good for him, not so good for the hangers. You’d better find the answer because uncovering anywhere from $250 to $1,200 in waste is typical in production units and even more in custom homes. There are two ratios that every builder should track for each model, yet no one does (note: for both ratios, leave out any amount purchased and installed in a garage):
A. Design efficiency: Square feet of drywall applied to walls and ceilings / square feet of living space. This ratio shows how carefully details are taken into consideration to get the greatest yield on material in the design stage. The ratio will usually be higher for smaller homes, although high ceilings, foyers, and cathedrals can throw that off. But when you find two models of similar size with substantially different ratios you’ll have an object lesson in the elimination of waste through Lean design. Study it thoroughly. No more 9-foot, 3-inch walls or 12-foot, 2-inch bedrooms.
B. Material yield: Square feet applied to walls and ceilings / square feet of drywall purchased. For clarity, express this one as a percentage. The ideal of course is 100 percent, and although that may be impossible, every point you fall below that is a quantitative measure of waste. If your ratio is 0.85, then 15 percent of what you purchased is waste, and for those who pay for labor by the sheet (a very bad idea) you also squandered 15 percent of the labor cost. Remember though, this is not all on the heads of your installation crews. If you don’t take the time and trouble to buy the board in the proper sizes, their ability to control waste is compromised. Measuring and tracking these ratios over time is not difficult, and significant savings will accrue.
12. Paint. This is a tougher one because it’s all about process. It is generally accepted that finish painters make one trip for prime, one for finish coat, then at least three trips for touch-up, for a total of five trips. More often than not, however, detailed tracking of trips reveals extra trips for touch-up. Our experience says a national average of seven trips is conservative, and although these extra trips are never charged by the painters directly, the cost is buried in their overhead, and in Lean, every penny counts. The minimum total cost for a return trip for the painter exceeds $100 and with opportunity cost, is closer to $150. Shouldn’t we do everything possible to cut trips down to three or four per unit? Saving three trips means saving the painting contractor at least $300. Achieve that and watch his price come down in the next bid.
13. Cabinets. Here’s an easy one: Get rid of Lazy Susans. Sorry Sue, but your days are over. You are a first-rate pain, a maintenance nightmare, and a collector of kitchen paraphernalia that could be better stored in a corner cabinet in half the space. Put a double-hinged door on it for easy access and you just saved $175, and no homeowner will ever hold it against you.
14. Flooring. I watched in amazement recently as a flooring contractor gave a primer on how to lay out carpet and solid-surface flooring to save 10 to 15 percent on the total bill. The builder was impressed and noted that his other supplier, the one that had 75 percent of his business for years, had never done an analysis or layout anywhere to that depth. The builder is now saving hundreds of dollars per house and the flooring contractor is on his way to getting all the business. The lesson is you can get a great price per square yard (or foot), then lose it on layout and installation. Find a supply partner who knows all the tricks. Hint: Give the same plan to multiple companies and ask them to do a detailed layout. There will be significant differences, and that means money.
15. Doors and windows. A thorough analysis of window and door sizes for standardization opportunities nearly always produces dollar savings without hurting the house in any way. Watch out for the details, like placing an arched decorative window on the side of a house where no one can see it or placing windows too close to the floor or too near a door, requiring tempering that could easily be avoiding. It is not unusual to find rooms with windows too large or numerous that furnishing becomes a challenge. These simple steps can save hundreds per house.
16. Siding. Rout out a channel on the back side of a flush rake or use a 2x6 over a 2x4 and eliminate most of the j-channel from a house. Reducing roof pitches and building in even increments saves siding, as well as framing, sheathing, and house wrap. There are two purposes for frieze board: to decorate and to cover up bad workmanship. Too often, they are larger than needed, making the roofline look heavy. Many designs simply look better without any frieze board at all. Attention to these small details can add up to several hundred dollars per unit.
17. Brick/stone/masonry. Stone looks cool, for sure. But an equivalent amount of stone on a typical house costs $300 to $500 more than brick. Will the customer pay for that? If so, great, but challenge yourself with that question. And if you use brick, consider queen size over standard for both labor and material savings. The first couple will look strange, but you get used to it quickly, and in some markets it’s all you see. Will your brick supplier sell you straps instead of full cubes? If not, find one who will. It’s ridiculous to be forced to buy 300 bricks to get the last 100 you need.
18. Flatwork. One more easy one: Get rid of driveway flares. What they get you are cracks and rework. Strangely enough, when flares are present, people tend to be even less careful when turning into driveways and they end up running over the lawn.
19. Landscaping. When dealing with live inventory, planning ahead means everything. Sit down with your landscape contractor and tightly estimate the material you need six to eight months in advance. They’ll be able to purchase more fitting product in greater quantities and pass on the savings.
20. Trash removal. After more than 20 years of dumpster diving, I’m convinced that high-side dumpsters do not just conceal waste, they create it. Take any overflowing high-side and ask your hauler to dump it out across a couple of vacant lots. Sort through it and you will be shocked. Finding $300 to $500 worth of perfectly useable material is the norm. If you’re not willing to go to a “yard pen” system, at least switch to low-side dumpsters. You’ll be astounded that even with the reduced capacity, you won’t have any more pulls than you had before. I will let you to ponder just how that could be.
In reality, there are more than 50 ideas buried in these 20 categories, and none of them qualify as “tricks.” Perhaps the biggest trick of all is to create the Lean mindset — the continual pursuit, identification, and destruction of all forms of waste in product and process. Anything that does not produce true value, anything that an educated customer would not willingly pay for, is waste. It requires a resolute commitment to sweating out each item and getting your management and construction practices nailed down. There is $5,000 per unit available in just these areas cited here, and a lot more where that came from. Nothing up my sleeve. No magic. No tricks.
About the Author
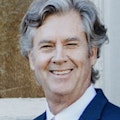
Scott Sedam
Scott Sedam is president of TrueNorth Development, a consulting and training firm that works with builders to improve products, process, and profits. A senior contributing editor to Pro Builder, Scott writes about all aspects of the home building business and won the 2015 Jesse H. Neal Award, business journalism's most prestigious prize, for his commentary in Pro Builder. Scott invites you to join TrueNorth's Lean Building Group on LinkedIn and welcomes your feedback at [email protected] or 248.446.1275.