A roof can represent 10-25% of the cost of a building, 90% of improper installation procedures are covered from view upon completion of work and defects are not identified until leaks or other problems occur at a later date, which brings us to the fact that roof failures feature high in construction litigation. Bottom-line doing the job right the first time is the way to go!
The most common deficiencies found in metal roof inspection are:
(1) Fastener back out
(2) Panel damage
(3) Leaks
(4) Seam defects
(5) Missing or damaged fasteners
(6) Corrosion
These arise from 5 common causes:
(1) The incorrect selection of product
(2) Poor waterproofing and installation
(3) Lack of trained and experienced installers
(4) Installation not consistent with manufacturer’s instructions and procedures
(5) Lack of quality control inspections and oversight.
Time spent at this planning stage is not wasted! The majority of problems can actually stem from the wrong design or incorrect product being specified during the design stage. At the design stage live loads, dead loads, snow loads wind loads, thermal impacts and rainfall levels need to be considered, membrane components, flashing, sequencing of installation and other trades all need to be discussed and agreed upon.
Ensure that all those involved agree with what is designed and understand the problems and logistics involved will prevent problems during and after construction. Often defects occur when other trades are working on the roof or when changes in design suddenly involve a new pipe penetration through the roof or the poor storage or handling of roofing components.
There should also be regular inspection of all material and equipment on arrival. Delivery, storage and handling instructions are also essential, explaining stacking on pallets the need for weather tight ventilated covering, the problems of storage with other materials that can occur such as staining, denting, bending, warping and twisting of materials and components should be highlighted. Waste due to damaged material is a huge cost issue.
Pre-construction inspection is also needed, to review the job site prior to starting work. Has all the other work been completed correctly so that you can start work on time, this includes all structural and non- structural components. Ensure any problems are raised and recorded prior to you starting work.
In process inspections are critical because once work is covered up it cannot be checked again, and most defects are only found when leaks and other problems occur.
Final inspection. Remember the majority of the work has now been covered up, you will be relying on the pre and in process inspections to have caught any errors, this is a final check on obvious and visual issues. However, this also means there is no reason for overlooking something at this stage such as missing fasteners or flashing.
Debrief. At the end of every project there should be a debrief, find out what worked well and incorporate that into your process or if something didn’t work well ensure you find a solution.
Customer and trade feedback. Do you know what your fellow trades, your client and the owner of the building actually think of your work and what it was like to work with your team. Many forget this stage. Create a simple survey and sit down and talk with your contractor to learn what went well and how you can improve. I have seen companies rehired for other work simply because they cared enough to ask this question.
In each of these inspections a detailed checklist is key to ensure your records are accurate. A simple tool to record all inspection stages is that of digital photographs and video. Digital storage and back up is easy today and these are excellent ways in which a picture tells a thousand words. Video key component parts, noting with a simple sheet of paper the exact location of the component and the time recorded.
To have a good system in place you should have a detailed Scope of Work that links to specifications, drawings, details, cross sections, photographs and of course manufacturer’s instructions. These should cover flashing details, fastener applications, eaves drip or fascia details, screw patterns, gutters, downspouts, purlins, rafters, roof hatches, pipe penetrations as well as instructions on sealants for example. They should also include examples of correct and incorrect installation which are key learning tools.
About the Author
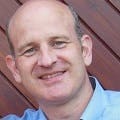
Denis Leonard
Denis Leonard has a degree in construction engineering, and an M.B.A. and a Ph.D. in quality management. He is a Fellow of the American Society for Quality and has been an Examiner for the Baldrige National Quality Award Board of Examiners, a Judge on the International Team Excellence Competition, and a Lead Judge on the National Housing Quality Award. He has experience as a quality manager in the home building industry as well as construction engineer, site manager, and in training, auditing, and consulting with expertise in strategic and operational quality improvement initiatives. His work has achieved national quality, environmental, and safety management awards for clients.