As we recover from the holidays and look back on the year, it appears we should all give thanks that 2013 has shaped up to be a pretty good year for residential construction and the economy in general. Depending on what you count, and which source you use, our industry and those that service it contribute between 11 – 15% to the Gross Domestic Product (GDP). In fact, our industry is expected to place in service approximately $340,214,000,000 worth of construction for the 2013 calendar year (U.S. Census Bureau, 2013).
Although the industry is relatively large in size and impact, the participants are highly fragmented: The Top 10 builders by volume only control 26% of the market for residential construction.
The industry fragmentation bears a stark contrast when viewed through the eyes of the automotive industry leaders as shown in figure above (WSJ, 2013). From a comparative standpoint, the Top 5 manufacturers of automobiles control approximately 70% of the U.S. market. The implications of this difference cannot be overemphasized. Can you imagine the level of integration that must exist between the players in that industry compared to ours? What kind of impact does that provide on the total purchase price of new vehicles in the U.S? Also, how would that level of integration with vendor partners change your competitive landscape as a builder?
As we all know, homebuilders tend to outsource many of the homebuilding activities to subcontractors and other supply chain partners for a number of very good reasons which we won’t delve into today. However, Nicola Costantino and Roberto Pietroforte reviewed the cost structure of construction activity and found the most commonly occurring costs associated with subcontractors involved coordination, inspection, and supervision which presented themselves in 100%, 70%, and 60% of the observations respectively (2002). Furthermore, many practices used to support the industry were adopted after World War II during an unprecedented demand for new housing (Taylor & Bjornsson, 2002). Taylor and Bjornsson’s study also shows that labor and construction materials account for in excess of 50% of the costs associated with building a home (2002). Therefore, delays in material can affect both the cost of material and the overall cost of labor which may remain idle during this timeframe. Through integration and the appropriate use of systems, automated demand planning could reduce any negative impact on profitability, product availability, and resource scheduling.
Studies show the industry has historically rejected change and adopted hard-handed negotiating techniques with respect to its suppliers. These characteristics lead many organizations to look primarily at acquisition cost for labor and materials without contemplating the overall impact to schedule, quality, or total cost to place in service (Leonard, 2010). In reviewing its data over the last several years, Hyphen estimates that over 2,000 companies that historically supported home builders (suppliers, subcontractors, distributors, etc.) either no longer exist or have left to support other industries. That estimate has been validated by countless builder testimonials that describe the struggle to find qualified and talented business partners to construct homes, especially in hot markets.
One study that modeled the residential construction supply chain noted that 83% of private subcontracting companies servicing our industry had 3 or less employees and 98% had 24 or less employees (Cheng, et al., 2009). If these statistics haven’t changed, what implications does this have on the systems deployed by those companies helping builders to construct homes in a timely and efficient manner? How are you providing information to these trades to enable efficiencies in their production?
If we want to gain efficiencies and reduce waste (unrecognized savings and potential profit), we must focus on the interactions of organizations viewed as a system as opposed to just the behavior of any one enterprise. Adrian Done asserts that there exists a gap in the research, especially within our industry, with regard to supply chain management. He believes that many studies have concentrated on intra-organizational operations while leaving many of the complexities of analyzing the chain of organizations that create the end product largely ignored (Done, 2011). When looking at your own enterprises for efficiencies, do you consider how the changes you employ (or refuse to) affect the rest of the supply chain? Do you just hope your changes are “good” for everyone? Given the large percentage of costs associated with entities outside the homebuilder, it might be advisable to be inclusive of your trade base when planning changes.
Jack Cheng and Kincho Law argued in favor of this extra-organizational view of the supply chain for the residential construction industry and contend that although the industry could benefit from integration, it remains largely unintegrated due to several reasons. The lack of integration between builders and their trade base costs the industry almost $16 billion dollars annually and may be caused by several factors including the high degree of fragmentation, the small size of suppliers, and the very temporary nature of the projects when compared to other industries (Cheng & Law, 2009).
According to a study performed by Cheng, Law, Bjornsson, Jones and Sriram, delays in completing activities by subcontractors cause daily rescheduling activities which ultimately lead to continual failures and additional rescheduling efforts. The rescheduling activities also impact product availability which is also taxed by the poor communication tools employed by some industry participants to distribute information (Cheng, Law, Bjornsson, Jones, & Sriram, 2010). In the simulations performed by Cheng et al., many of the communications can occur automatically and instantly through the use of an integrated solution (2010). I believe they were right on the mark as Hyphen has used a similar technique with various business partners to automate activities over 10 million times this year alone. Builders have the opportunity to improve accuracy, speed, and operation efficiency while reducing costs by up to 75%.
Over the next few weeks, we will further explore the idea of reducing transactional costs in the home building supply chain. Please plan to visit Hyphen Solutions at our booth (C3153) during IBS 2014 (February 4-6). In the meantime, www.hyphensolutions.com.
Editor's Note: This content is sponsored
About the Author
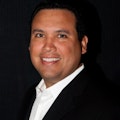
Felix Vasquez
Felix Vasquez is the President and Chief Technology Officer of Hyphen Solutions, LLC., whose software is used to build approximately 100,000 homes annually. He has held this position since 2002 and been instrumental in Hyphen’s product strategy and business partner development which includes the world’s leading manufacturers and software providers. Prior to joining Hyphen, Felix was Vice-President and Chief Information Officer of D.R. Horton, Inc. where he worked on IT Strategy and Alignment, Business Process Optimization and Supply Chain Improvement. Felix’s background includes roles of increasing responsibility at companies such as Du Pont, EDS (now Hewlett Packard), and IBM. He holds a BSCS, an MBA, and is currently a Ph.D. candidate in Systems and Engineering Management with research centering on residential construction supply chains.