Project Manager Workloads: How Much Is Enough?
Last month, the same question came up in discussions with two different production builders on opposite sides of the country—and opposite ends of the building spectrum: “How many homes can a field superintendent carry?”
One company builds 100 large, “high-bling” units with tons of options and is fully amenable to custom options, even structural. The other builds just over 500 starter and first move-up units with a strictly defined list of options and selections and no custom options, especially structural. Right there, it’s clear the answer for each of these two builders will be quite different.
I have a long history with this question and have pondered it seriously about every other year for the past few decades. My company, TrueNorth Development, is well-known for creating Excel templates that help builders get a handle on little-understood yet critical measures that drive production and cost.
One example is our “Saved Day Calculator,” which measures the full impact of a schedule day. Another is our “Trip Cost Calculator,” which exposes the true total cost of trips to building sites by suppliers and trade contractors, revealing a monumental financial impact.
RELATED
- Lessons Learned as a Field Supervisor [VIDEO]
- Roll Up Your Sleeves and Get Serious About Cycle Time
- How to: Management Tips to Keep Your Team Together
I had a plan, which over time became closer to just a dream (and is now more like a mere fantasy), to create the “Superintendent Load Calculator” in which a builder enters all relevant factors and “Voila!” the formula spits out the answer: “Based on your inputs, this superintendent can effectively manage 16 units-in-process.” Our builder clients, or potential clients, would be totally amazed, and we’d have to install another phone line in the office just to handle the calls for consulting help that would pour in.
Untold years and attempts later, the goal still eludes me. I don’t have a concise formula and I can’t give you a number, but briefly laying out all of the factors toward that goal is a worthwhile exercise and will help you identify the appropriate range—if not the exact number of units—your field superintendents can handle.
Work through the following list to see if your assumptions about how many homes your field supers can manage measure up.
Note: Front-line field superintendents are known by many names, but for this column, I’ll refer to them as project managers or PMs.
Factors That Affect Field Superintendent Workload
1. Experience/expertise
This seems obvious. A project manager with 20 years’ experience should be able to handle more units than one with five years on the job. Yet we’ve all seen cases where the opposite is true. Some learn from experience, some don’t ... and many learn the wrong things. A few years’ experience is better than little or none, but what a PM can handle doesn’t closely correlate to that metric.
Also consider where the experience originated. PMs moving from custom building to production operations take longer to adapt, and the reverse also is true. Similar hurdles are found switching PMs from single-family to multifamily and vice versa. Finally, the way a company builds and operates can differ dramatically from builder to builder. Thus, five years’ experience at your firm may count for more than 15 years with another builder.
2. Training
Following on from the factor just mentioned, not everyone learns from training. Yet companies with a well-developed, highly focused training process in both “soft” and “hard” skills for project managers create more capacity. Their PMs will almost always succeed at carrying more units.
3. Quality/level of trades’ experience
Do you have solid, well-developed partnerships with suppliers and trades that know your company, its methods and plans, and have worked productively with your team for years? Or do you churn and burn through trades, always looking for a lower bid price? Which scenario will enable your project managers to manage a higher volume of product? You know the answer.
4. Type of units/design
Do you build starter homes? Move-ups? Custom? Single-family? Multifamily? And for each of them, how many square feet and how complex? Are they “box-on-box” with perfectly straight foundations, walls, and simple rooflines? Or are they festooned with pop-outs, cantilevers, bays, bows, eyebrow returns, porticoes, fake dormers, and multiple roof breaks? Now add to that: foundation type. Monolithic slabs are easier. Post-tension slabs, more involved. Crawlspaces take more time, and basements the most of all. Add difficult soil conditions to extend the time even more. All of these factors and their relative complexity affect how many units project managers can manage simultaneously.
5. Amenities, options strategy, custom options policy
No matter the type of home you build, higher amenity levels require more time to manage. A huge design center offering a vast number of options and selections for high-bling homes puts additional burden on a project manager. Structural options further increase the load. Finally, do you allow custom options? You can guarantee a builder that accepts custom options, especially if structural, can’t expect its PMs to carry as many units as those that do not.
6. Late-change tolerance
This factor is cited separately because so few understand the negative impact late changes have on the construction process and schedule, not to mention the strain they place on Purchasing and Estimating. Virtually all home builders have cut-off dates and a late-change policy saying, in so many words, “We don’t do that!” But very few actually follow their policy. Your PMs pay the price, as does your schedule, and your profit.
7. Spec vs. contract homes
In some U.S. markets 75% to 80% of homes are “spec units” and there are even some builders that build only spec homes. This strategy takes more capital and carries greater risk, but life sure gets easier in the field when all selections are predetermined and there are no customers to manage during construction.
In other markets, contracted sales make up 75% to 80% of volume and there are a multitude of other possible combinations. Theoretically, if all options and selections are made on time, there are no custom options, and the “no late change order” policy is actually followed, building a contract home is effectively no different from building a spec home.
No matter the type of home you build, higher amenity levels require more time to manage.
But anyone with field experience reading this is either rolling their eyes or throwing a chair across the room because it simply doesn’t work that cleanly. Contract homes require more attention from the project manager than spec homes do—unless, of course, your own people make constant changes on your spec units, which is a discussion for another column.
8. Proximity
It’s completely obvious that a PM building right down the street in a single project can handle many more homes-in-process than one who drives miles between multiple sites or is building widely scattered units across a single large project. Just be sure to include this reality in your calculation.
9. Internal office support
The level of internal office support for and cooperation with the PMs varies significantly from builder to builder. Consider land development, design, sales, purchasing, warranty, and administrative functions. Some make life easier for project managers, some make it more difficult. Be brutally honest. On a one-to-10 scale with “reliably helpful” at the top and “predictably obstructive” on the low end, where do your internal departments fall? The result will have a lot to say about how many units your PMs can carry at one time.
10. Field support/service and warranty structure
This can be as simple as having someone to chase down permits, so the project manager doesn’t have to do it, to having a “field secretary” who manages all plans and paperwork at a large site, to a dedicated service and warranty department to take the burden off the PM for that part of the process.
At times, you see an “assistant project manager” role to help with the day-to-day on big projects. Some builders will split the work between front-end and back-end PMs. In some companies, you may see a customer care person who does the final walks with new homeowners so the PM doesn’t have to. There are as many variations here as there are builders, but the more help available, the more homes the PM can manage.
11. Start-package detail, accuracy, and variance
You may call it by a different name but the “start package” is the set of documents that tells all suppliers and trade contractors, without exception, exactly what goes into a home before construction begins. The package includes final plans, options, and selections—all specifications and their agreed costs. Anything less and you’ll pay for it, over and over, in variance costs ... and lost time.
If you ask me to pick just one factor to help a builder determine how many units a project manager can carry simultaneously, it’s cycle time.
I almost hesitate to advise using your variance level (VPO, FPO, EPO, etc.) to help determine how many units your PMs can handle because, in my experience, it’s incredibly rare to find a builder that calculates variance fully and accurately. Simply, the higher the variance level, the more burden on your PMs, and the fewer units they can handle. And note: The load on the PM increases exponentially, not arithmetically, with increase in variance. Double the variance and you’ll far more than double the negative impact on a PM’s workload.
12. Adoption of off-site methods
Off-site vs. on-site methodology is one of the hottest issues in the industry. Presuming a dependable supply chain, off-site methods reduce on-site labor and cycle time to a significant, if highly variable, degree, when effectively utilized.
There are simple off-site components such as stoops, dormers, stairs, window casing and trim, and doors with jambs and casing, while roof trusses and open wall panels are more involved. Closed panels, structural insulated panels, roof and floor cassettes, and preformed or panelized foundations take it to another level. There is a learning curve, but once a builder crests that hurdle, off-site solutions increase the number of units a PM can handle.
13. Technology
Almost all builders have one of the well-known software packages to manage everything from back-office accounting to scheduling and everything in between, or they’ve developed their own system. But the number of builders that keep the databases up to date, train everyone on how to use them, and fully use the system capabilities to run the business is rare.
Where we encounter this situation most often is the schedule portal. Simply put, the continual feedback from suppliers and trades in our Lean implementation work is, “We cannot and do not trust what the portal schedule tells us.” As a result, they scout sites—at considerable expense—to see if the site is truly ready, and they deluge the PM with phone calls and texts. Suffice to say, a fully accurate schedule via an online portal can lift considerable burden from PMs.
RELATED
- 7 Steps to Building Homes Faster
- Data-Driven Builders Leave the Guesswork Behind
- Cycle Time: the Gift That Keeps on Giving
14. Weather
This is one I am loathe to highlight because it is too often used as an excuse. Many times I have seen builders in the Northland build faster and more efficiently than those in more benign climes. I had to bring up official historical weather data to convince a builder from Alberta, Canada, that Minneapolis is actually colder in degree-days during December, January, and February than his location. Yet the hearty builders in Minneapolis managed to build more effectively throughout the winter. Weather remains a factor though, and wind, rain, snow, ice, and heat are also part of the equation.
15. Cycle time
I saved this critical element for last because it is so typically overlooked. In fact, if you ask me to pick just one factor to help a builder determine how many units a project manager can carry simultaneously, it’s cycle time. If I build in 180 days and you build in 90 days, your PM can complete twice the units in a year as mine. Or, you can build the same number as me with half as many PMs. The math is both simple and compelling, while the logic is obvious.
If I take 180 days, I have houses piling on top of one another and there is simply no way to follow the old adage for PMs to be in “every house, every day.” I know in these times of continual trade and materials shortages, maintaining a tight schedule is far tougher than it used to be. Ninety-day schedules—relatively common before the big crash 15 years ago—are rare today, yet they do exist, and it can be done. So, start with wherever you are today, and find one day, then another, and another. Soon your PMs will be able to handle more homes.
You’d like this to be simpler? Me too. So, tell me ... which one of these elements is not a significant factor in the equation for how many units a project manager can handle? Sit down with your team and evaluate the current load you place on your PMs. Start with a simple “+, 0, –” representing positive, neutral, or negative for the current impact of each of the 15 items on this list. When you have your answer, or perhaps you’ve identified some additional factors, please email me at [email protected]. I still hope to develop the magical “Superintendent Load Calculator” template someday. Your input could help.
About the Author
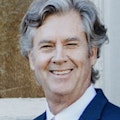
Scott Sedam
Scott Sedam is president of TrueNorth Development, a consulting and training firm that works with builders to improve products, process, and profits. A senior contributing editor to Pro Builder, Scott writes about all aspects of the home building business and won the 2015 Jesse H. Neal Award, business journalism's most prestigious prize, for his commentary in Pro Builder. Scott invites you to join TrueNorth's Lean Building Group on LinkedIn and welcomes your feedback at [email protected] or 248.446.1275.