Less Waste, More Profit in 10 (Not So Easy) Steps
Who among us has not seen the ubiquitous web ads proclaiming a miracle solution to whatever ails you, from obesity to high blood pressure, using this “one weird old trick”? Well, I have one for you, and with it the U.S. home building industry can bank more than $100 million extra in 2013. Furthermore, my trick can launch a process to net more than $500 million annually if builders decide they want it bad enough. The latter figure will take some work, but the initial $100 million requires not one new hire, new software, change in product, or even a visit from a consultant. It is so simple that many will find it difficult to believe. Ready? Simply paint every dumpster in America bright green, add big gold dollar signs to the sides, and then apply placards that read, “This Dumpster Reserved For Builder Profit Only.”
You’re probably kicking yourself because you did not think of this sooner, right? Okay, maybe not, but I have worked with builders in the field for 25 years in multiple countries and continents, and though I have not seen everything, I have seen a lot — enough to guarantee this one simple move will save 20 percent of your site waste bill in 2013. The numbers are real. The lastest figures available from the NAHB indicate that waste removal cost averages $1,200/unit nationwide.
Those costs will grow as landfill space shrinks and moves further out while increasing regulations determine what goes in landfills and in what form. Removing 20 percent produces $240/unit. At the predicted rate of around 500,000 units in 2013, that totals $120 million of the $600 million waste removal bill for home builders nationwide.
Would painting the dumpsters actually make a difference? Yes, because of one simple fact: management would finally start paying attention. If builders had to stare in the face each day the reality that every single item in a dumpster, including the neighbor’s couch, represents money right out of their pockets, they’d get seriously annoyed. Each dumpster they saw going down the road would be screaming out, “I’m taking your money to the dump and you can never get it back!” Then they’d get seriously involved. The Hawthorne effect itself — simply giving an issue extra attention — would take us 20 percent of the way there. Not only would company owners get annoyed, so would site managers, suppliers, and trades.
I fully understand the slim odds of getting Waste Management and BFI to paint their dumpsters bright green with gold dollar signs, but you can create the same impact through an awareness campaign and making dumpster inspection a weekly ritual. It’s the thinking that counts.
Since now we know that upwards of $600 million is at stake, it is clear that a “paint the dumpsters” strategy is not merely impractical but insufficient. Besides, the best builders at this game have forgone dumpsters long ago. So let’s presume your management team is now both aware and motivated. They want to knock that waste bill down from $1,200/unit to $200 and save $1,000 per house. Where do you start?
First, lay aside your gut instincts that yelling, threatening, cajoling, and writing memos telling employees, suppliers, and trade contractors to “stop being wasteful, damn it!” will accomplish anything. What’s required is a significant culture change that begins with senior management and flows right down through the ranks to the guy dropping a nice clean brick off the scaffold, into the mud. That culture, with good tools and techniques, will get you there. Start with this outline and build your own model.
1. Create Your Site Waste Reduction Team
Tackling the monumental challenge of site waste reduction requires cross-functional input, from design to estimating to purchasing to construction. It is simply too big for one or two employees working on their own to get their arms around. Create a team with strong, senior leadership, empower them to challenge the status quo, and make them responsible for results. Reinforce them continually.
2. Establish Current Waste Baseline and Calculate Material Yields
How much are you really wasting? How much is normal? Without establishing metrics you’ll find this highly subjective. You must establish “objective current reality” before launching any improvement effort beyond simply “everyone pick up after yourselves.”
How much of the concrete, wood, roofing, wire, plastic, tin, siding, brick, stone, insulation, drywall, vinyl, paint, carpet, tile, etc., that you purchase actually ends up in your house? Does it vary by trade contractor? By model? Community? Superintendent? Doing this right requires significant detail, so start with one community or just one house if you have to. Remember, every single thing that finds its way into those dumpsters (other than the neighbor’s couch) is something you paid for, and now you are paying to have someone haul it away and bury it. Even that couch is costing you, as part of the pull charge.
3. Analyze Key Waste Sources in Your Home Building Process
Once you have identified and quantified the waste, look for the sources found in plans, specifications, process, methods, and labor. For example, take a look at the pile of drywall waste depicted in the picture above. The source could be any combination of:
• Bad design. For example, having a 12-foot, 2-inch x 12-foot, 2-inch bedroom or a 9-foot, 3-inch garage wall.
• Bad purchasing decision. For instance, a great deal on 4 x 12-foot sheets, creating waste by not sizing per room/area.
• Bad buying practices, such as paying labor by the sheets purchased, not by the square feet applied.
• Bad installation, like hanging the closets and pantries first.
All of these and many other possibilities abound, but you will not know without good analysis. A note of caution: source is not always the same as root cause. Local purchasing, for example, might know that 4 x 12-foot sheets are not optimum for one particular plan or series, but they’ve been forced into it by a national contract.
4. Analyze Scopes of Work
Scopes must say more than simply, “pick up after yourselves.” Scopes must clearly define standards of job ready/job complete with details for cleanliness, waste removal, minimizing materials brought to the site, and protocol for communicating material overages back to the builder.
Now comes enforcement, but rather than always catching people doing something wrong, place even more emphasis on reinforcing the right behaviors. Also, a strict policy of paying trades immediately for work done on time and when — and only when — 100 percent complete to scope is a superintendent’s best friend.
5. Conduct Analysis of Operational Practices in Your Home Building Company
All processes can produce waste, including:
• Scheduling
• Product delivery and placement on the site
• Site management
• Incoming quality and quantity audit against takeoffs and purchase orders
• Labor methods and application
• Waste removal systems (dumpsters, pens, site recycle, etc.)
• Feedback to estimators regarding overages
• Feedback regarding architectural variances
• Rewards and penalties for on-site waste control
6. Analyze Your Company's Purchasing and Estimating Methods
Overflowing dumpsters don’t normally turn our thoughts to office-based staff as a source, but their contribution can be significant. Product takeoffs provided by suppliers and trades alone, for example, always guarantee higher cost and more waste. Is there a specific waste-avoidance emphasis in the takeoff process? Is purchasing using feedback on quantities directly from the field? Do you depend on vendor “pick-ups” of overages that are either high cost, seldom done, or if done not credited? All of these add up to waste.
7. Obtain In-Depth Supplier/Trade Feedback
To solve the site waste problem, suppliers and trades have to be willing participants. Get them involved earlier in the design process and heavily in plan and specification reviews before the first model is built. Walk the sites with them. Count things together. Push together to determine every possible way to avoid bringing excess material to the site in the first place, then challenge methods that produce waste during construction. Now take everything you learned back to the scopes of work and your purchasing practices.
8. Implement Best Practices for Waste Reduction in Home Building
The following is a list of five sample waste-reduction best practices by discipline. As you get deeper into the process, develop your own list based on local parameters.
Anti-waste design best practices:
• Even dimensions and standard lengths
• Rule of the square (more efficient than a rectangle)
• Optimum placement of HVAC, electrical, and plumbing
• Reduce waste in interior design — hallways, circulation space, mis-sized rooms, poor space planning
• Reduce waste in exterior design — truss pitch (creating piggybacks), improper detail, redesigned pitch to use full sheets
Anti-waste purchasing best practices:
• Waste minimization as a key decision criterion (e.g., buying precision-cut I-joists instead of 2-foot increments)
• Rating each suppler and trade on waste by site
• Quantity variance audit and tracking
• Incentives for material, labor, and cycle-time optimization
• Use of off-site-built components when possible
Anti-waste field management best practices:
• Field audits for compliance
• Pack-it-in, pack-it-out policy
• Quantity adjustment hotline
• Eliminate dumpsters, especially high-sides
• Analysis of waste — ongoing
9. Recycling and Reuse Strategies to Limit Waste
With the caveat that it is far better to not produce waste in the first place, with whatever waste is left, are there any methods to redirect it to a productive use and keep it out of the landfill? Recycling opportunities vary by community. Do you know what yours are? I completely agree that trying to manage a cardboard dumpster on site is a near-impossible task. But it is not so hard for the vendors to take their cardboard back and manage it at their own site. Many builders have purchased grinders to process gypsum and waste wood and add it back to the soil. Some have been stymied by local regulations and others have found that it takes a minimum of volume to make it worthwhile. Whatever the obstacles, don’t give up. I fully believe that 10 years from now, we will look back amazed at what we thought we could not do in this arena.
10. Continual Improvement of Waste Reduction
One of the most impressive companies I have ever observed in this arena is Hearth & Home Technologies, manufacturer of Heatilator and Heat & Glo products. From their beginnings in Lean process around 15 years ago, waste has been reduced to miniscule numbers, saving them millions. The culture is obvious and pervasive, and techniques cover everything from minimizing inbound packaging to optimum use of materials in process to recycling pallets to material providers. If you visit them and pay attention, you will realize that for them waste reduction is not a project; it’s a way of working and a way of life. It is just what they do, part and parcel of the business of building fireboxes.
But continual improvement requires ongoing tracking and feedback. With the right process and attitudes in place, it gets far easier, but entropy is a law of nature that will not be denied. Without vigilance, disorder will creep back into process, and monitoring the metrics you calculated in step 2 is essential.
Is an 80 percent reduction in site waste really possible? That figure is common in a host of manufacturing industries, and there are builders who have that number in their sights, but you won’t find it without a strong team and a comprehensive, step-by-step approach that leads to permanent changes.
These 10 steps are not easy. No time or resources? Just multiply your closings by $1,000. That is what is on the table, not including your time and administration and collateral costs. Now ask yourself this: Might there be other savings that go along with a significant reduction in waste costs? What impact would it have on customers, suppliers, trade contractors, city inspectors, and your own people when your sites are clean, with hardly a scrap to be found? Can a 100-unit builder stare down $100,000-plus and really choose not to spend time or money to pick it up? Most will do exactly that — move on to something else. But if you have the determination to pursue it, you will create one more competitive advantage.
About the Author
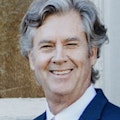
Scott Sedam
Scott Sedam is president of TrueNorth Development, a consulting and training firm that works with builders to improve products, process, and profits. A senior contributing editor to Pro Builder, Scott writes about all aspects of the home building business and won the 2015 Jesse H. Neal Award, business journalism's most prestigious prize, for his commentary in Pro Builder. Scott invites you to join TrueNorth's Lean Building Group on LinkedIn and welcomes your feedback at [email protected] or 248.446.1275.