Ways to Improve Home Building Productivity, Part 2: Automation
Part 1 of this series addressed how home building lags other industries in achieving productivity gains and how simplification and standardization are key to
3 Ways to Automate Residential Construction and Increase Productivity
1. Construction Automation
In my first job with a large-volume home builder, I saw firsthand the value of making as much of the house—wall panels, roof trusses, floor systems, stairs, millwork, and other components—as possible in a factory-controlled setting and delivering them to the jobsite on a just-in-time schedule.
Consider the potential benefits of off-site construction to your current home building process. Efficient off-site construction works like an assembly line: It doesn’t require skilled framers to know which material goes where and how to fasten it, while the equipment’s technology makes precise cuts and identifies fastening patterns. Modern manufacturing equipment uses material optimization software, laser-etching technology to mark intersecting stud and plate locations, overhead light curtains to illustrate truss intersections, and bridge nailers to place a dozen-plus fasteners at once, among other material- and labor-saving innovations.
RELATED
- The Road to Simplicity in Home Building: A Way of Thinking and Operating for Business Success
- Your Road Map to Off-Site Construction and Modular Homes
- A Case (Study) for Off-Site Construction in Home Building
And material left over can be saved for future use rather than ending up in the dumpster. For example, when I worked in a component plant, any 2-by-4 or 2-by-6 more than 4 inches long would be used for cripples in a rough window opening; shorts from 2-by-4s and 2-by-6s can be turned into full-height wall studs by finger-jointing.
Employing off-site construction methods also helps to minimize risk of:
- Materials on site being exposed to the elements and going through multiple wet/dry cycles on the jobsite, risking potential warping and mold damage;
- Someone framing the house wrong;
- Theft, since there’s a much better chance of 2-by-4s walking off the site than a stack of wall panels going missing.
Additionally, off-site construction methods can improve your cycle time, reducing your interest to carry a construction loan and minimizing your opportunity cost.
So, why aren’t more home builders using off-site construction methods to realize greater productivity?
The biggest hurdle to home builders adopting off-site construction methods and realizing productivity gains in home building is the perception that off-site costs more than stick-building. If you’re serious about it, conduct a true, total cost comparison between the two methods working closely with a trusted off-site provider to understand your needs, to rework your plans to suit a factory setting, and to bid the job competitively for a fair, honest assessment.
And when you find a good off-site manufacturer, bring them into your business as a strategic supplier and have them participate in your new-product development.
2. Back-Office Automation
Automation isn’t limited to off-site manufacturing. Artificial intelligence (AI) tools to improve home building productivity are developing quickly to help boost your back office’s efficiency.
For instance, rather than simply dumping data into your enterprise resource planning system, use software that maps specific fields and can upload thousands of rows of data in seconds.
Similarly, consider building digital exception reports that identify potential data inaccuracies in your quality assurance processes and automate your procure-to-pay system to save you and your suppliers and trades a ton of time.
Scheduling software gives you the ability to run rough-cut capacity scenarios to identify bottlenecks and reduce cycle time, while using blanket purchase orders instead of one-offs streamlines recurring purchases. And, as discussed in Part 1, you can use software to simplify and standardize specifications. The technology is available and proven.
3. Vertical Integration
If you have the scale, consider vertically integrating off-site manufacturing. It’s an expensive venture but if you compete with one of these builders, you know the competitive advantage they enjoy. That integration means they have shorter cycle times, less waste, less labor, better quality, and cost efficiencies ranging from fewer dumpster hauls to preferred pricing through high-volume, manufacturer-direct purchasing. If you weigh up the advantages that result from having control over more of your production process—especially given current labor shortages—it may prove to be worth the investment.
It all comes back to simplification and standardization to improve productivity. Unless absolutely necessary, resist the urge to design a new product altogether. It’s better to rework and optimize existing plans as often as possible. Reworking plans for efficient constructability helps reduce warranty work and costs, plus it will earn economies of scale associated with plan reuse and SKU minimization, among other advantages.
And make it easier for your team to reuse those plans by having a common location on your network where everyone can see floor plans, costs per square foot, sales statistics, warranty records, cycle time averages, customer satisfaction feedback, and material quantity take-offs—in short, the whole picture.
The housingOur industry must address its lack of productivity gains to truly solve the housing affordability crisis. We owe it to our business, our employees, and our country to attack the challenge head-on.
About the Author
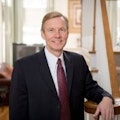
Tony Callahan
Tony L. Callahan, CPSM, CSCP, has worked in the home building industry for nearly two decades and is an expert in purchasing and supply chain management.