Being on an active building site at 7 a.m. as it wakes up for a new day of construction has always been a special time for me. I don’t expect everyone to appreciate this as much as I do, but I know that many of you understand. I suppose it’s one of those things you either get or you don’t, and there is certainly no shame in the latter. Yet, if you have not witnessed the awakening of a busy project, I suggest you put on some old shoes and go out to observe this phenomenon on some bright morning.
There are always the early birds on the jobsite — maybe the plumber unloading his truck, a roofer hauling some ridge vent up a ladder, or a concrete truck spinning its way down to lot No. 72, where the crew awaits the first pour. Meanwhile, all across the city there are other activities soon to converge on this site at some point during the day — trusses going on the flatbed for lot No. 45, cabinets into the panel van for lot No. 60, and a couple of HVAC guys bending tin at the shop to save time later on lot No. 57.
When a site is truly well run, you can feel it almost instantly upon arrival. It’s a joyful thing to behold with everyone busy, making money, and working together to produce a well-built home that some family is going to love. And then there is the bonus that you get to do all of this outside, not chained to a desk with your cerebral cortex seemingly hard-wired to the ubiquitous PC.
A Construction Jobsite That's Getting It Wrong
On one such morning earlier this year, I anxiously anticipated my early arrival at a project where sales had been unusually strong. It sounded like a return to the good ol’ days of 2006, when multiple homes progressed in various stages of construction within the same development. What I found was indeed a very active site, but it did not require a particularly hard look to discover that so many of the people on the site were extremely busy — doing the wrong things. I watched overflowing dumpsters fed by Bobcats while a curb was dug out for repair. I saw three and four cubes of brick left over on finished homes while literally hundreds of full brick lay scattered around the lots. A mountain of drywall waste told a story that no one was paying attention.
Meanwhile, excess bundles of shingles were flung off a roof to the ground below, the packaging burst open to bring a final answer to the question: Would any of this excess be picked up and credited, and why the excess in the first place?
Inside the houses, an electrician punched holes through a wall in an attempt to find a buried box, all the while cursing the drywall finishers who had left at least two-thirds of the boxes full of “mud.” That requires time to cut out the excess and dig out the screw holes for receptacles and switches while creating a mess that someone now has to clean up. My shoes caught on OSB flooring seams that required grinding before carpet or flooring could be installed. The houses were festooned with excess cripples, jack-studs, king-studs, outsized headers, and headers not needed at all. I found oversized plumbing walls — evidence that either the plans were wrong, the plumber screwed up, the framer screwed up, or some combination of the above.
Following that theme, I saw a couple of nasty “collisions” between HVAC ducts and framing members, requiring jumpers that clearly represented an unnatural act.
Why So Many Quality and Process Problems on Site?
Let’s stop here and ask: How does this happen? I challenged myself with the same question that morning and my thoughts quickly harkened back to my old mentor, Mike Rhodes at Pulte Chicago, who I met nearly a quarter of a century ago and still speak with regularly. In my time, I have met a lot of great VPs of Quality, but only a handful could fully measure up to Mike’s standards and abilities. Recalling the list detailed above — and I hardly exhausted the unfortunate opportunities at that site — any one of them would have found the superintendent on the wrong end of a monumental butt-chewing from Mike. The collection of blunders cited here would have resulted in instant dismissal. Make no mistake, Mike would exhaust himself working with anyone who truly wanted to improve, but having that many sins was evidence that someone was just not paying attention. There may be a basketful of extenuating circumstances, but what I saw that morning was simply a bridge too far. I thought to myself, what would Mike do?
That was easily the worst site I have been on during the past year, but I have seen pieces, parts, and symptoms of the problem all across the country. But frankly, it’s really no surprise. In the six years of the downturn, we have lost most of the experienced field professionals over 50, as well as many of the best and brightest under 30. Those in the middle are now working double time, if not more. I empathize with anyone caught in this wringer, yet I can point to field superintendents who maintain quality standards despite the extra load. So what’s getting in the way of all the rest? We see it in our Lean implementations, which number nearly 100 over the past six years. The culprits include: plans described as inadequate, to be kind; specifications that are moving targets; and continual turnover of suppliers and trade contractors as purchasing relentlessly pursues another nickel per square foot, even if the evidence suggests it will cost them a dime in the not-so-distant future. All of this contributes to field superintendents’ inability to keep up.
Is there anyone looking at the big picture? Is there anyone monitoring quality and process? Is there anyone left to train the field? These are tough questions. All across the country, we see sales are up, but there’s a pervasive reluctance to hire additional staff. That’s understandable, as we now live in a world where the number of starts we’ll see next month can be influenced by what happens in Greece, Spain, Ireland, or Portugal. But in the meantime, let’s control what we can, and site quality is a great place to start. At this point you may be thinking, “Wait a minute ... Didn’t Scott just fire off a long list of mitigating circumstances that get in the way of site quality?” Absolutely. And by focusing hard on field-quality issues, you will bring these background factors quickly to a head. Now you can measure their impact, make a plan, and fix them.
10 Basics of Field Quality Management
Earlier in the year, Professional Builder published my three-part series on quality management, and this could rightly be cited as part four. There is so much to cover in this arena. But presuming your field quality status needs a review, here are the basics that any good builder must address:
1. Incoming quality inspection of materials. This seems to be a basic requirement in nearly every industry — except home building.
2. Supplier and trade selection. This cannot be the exclusive province of purchasing. The field has to be directly involved.
3. Scopes of work — applied. How many of those on your jobsites truly understand the definition of a completed job to your specifications? When was the last time you had a good discussion about that?
4. Schedule. There is simply nothing more important for the entire company, but the field superintendent is on the front line and must manage it every day.
5. Job ready/job complete. Each trade that arrives on site must find the job fully ready and leave with the job fully complete. Anything less is unacceptable.
6. Product quality. Clear standards are required for each component of the house, and checklists must be maintained by the superintendent, suppliers, and trades.
7. Site conditions and waste management. If the site is a mess, everything else is a mess as well. Customers intuitively know this. Site waste must be rigorously managed to the lowest possible level.
8. House cleanliness. A dirty, cluttered house indicates not just a lack of respect for the builder, but also for the other suppliers and trades. As a result, everything suffers, including quality, schedule, and cost.
9. Supplier and trade evaluation. Every partner must be evaluated on each house by the superintendent using established, known criteria, and tracked over time. Purchasing must use this data as part of their selection process.
10. Crew evaluation. Crews matter. They can make the difference between staying on schedule with 100 percent quality or not. Track them by name. Then demand that purchasing negotiate for the best crews, not just a gang of framers, roofers, or painters.
Is field quality truly a lost art? I’d call it more aptly an endangered species. There are, indeed, pockets of the industry where quality is alive and well. But if you hear the strains of David Bowie and Freddie Mercury singing “Under Pressure” in the background, your fears are well founded. Almost everyone is running short staffed, and if this recovery has staying power, by fall the field is going to need help or the consequences will be severe. If you hire young people, they need to be trained. If you hire experienced hands, they probably need retraining.
A solid foundation in the 10 elements of field quality is a great place to start. You may not have met Mike Rhodes, but chances are you have known your own version of him during your career. Ask yourself, “What would Mike do?”
About the Author
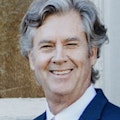
Scott Sedam
Scott Sedam is president of TrueNorth Development, a consulting and training firm that works with builders to improve products, process, and profits. A senior contributing editor to Pro Builder, Scott writes about all aspects of the home building business and won the 2015 Jesse H. Neal Award, business journalism's most prestigious prize, for his commentary in Pro Builder. Scott invites you to join TrueNorth's Lean Building Group on LinkedIn and welcomes your feedback at [email protected] or 248.446.1275.