After working a variety of construction jobs and for a large commercial lumber dealer in my youth, I cut my teeth after college at U.S. Steel, then Motorola—low-tech and high-tech manufacturing, respectively. I truly saw the good, the bad, the ugly, and the sublime.
At U.S. Steel, I learned anti-quality and how management was forced, if not always willing, to sacrifice longer-term viability for short-term profit. Yet on those rare night shifts when 100 of us made the largest structural steel rolling in the world just cook, it was a wonder to behold. Hot, dirty, dangerous, and exhilarating. That same mill supplied steel for the hulls of nuclear submarines and aircraft carriers, and structural beams for the Empire State Building and Hoover Dam, among countless other incredible structures.
RELATED
- Read part 1 in this two-part series: On-Site vs. Off-Site: a Total Cost Analysis for Home Builders
At Motorola, we were global leaders in the semiconductor and cellular phone revolutions and the go-to producer of communication systems for satellites. While immersed in rescuing the company from its dying consumer electronics business, I was lucky to meet most of the world’s foremost quality gurus including Deming, Juran, Crosby, Fiegenbaum, and Goldratt. Quick! Name just one individual today of that stature. Those were heady times.
Motorola was arguably the American leader in implementing Total Quality Management and was the first winner of the Malcolm Baldrige National Quality Award. Watching semiconductors glide down an assembly line and robots add layers of silicon and electronics was not as compelling as seeing red-hot 20-ton I-beams flying in and out of progressive roll-stands at up to 30 mph, but each had a rhythm and magic all its own. I’ve yet to find anything on a building site that compares to that kind of production. At this stage of home building’s evolution, we can only call our current efforts “manufacturing lite.”
So as an old manufacturing guy, I fully understand the capabilities and promise of applied manufacturing to home building. Yet I’ve seen many technology cycles come and go, each accompanied by a renewed promise to revolutionize the industry. It will happen and, in truth, it is happening now, albeit in fits and starts. But there are many practical obstacles such as the need for steady volume to support the capital outlay for off-site plants and more “social” hurdles in the realm of culture, change, and transition from traditional building methods.
Among the biggest barriers is that we’re simply not good at measuring the true total cost of on-site vs. off-site production methods. On our best days, we work at little more than a “bid price plus” level, with some consideration of other factors beyond the initial bid for labor and material. What we need is a deep understanding of “true total cost,” which includes costs of design, delivery, quality, waste, equipment requirements, warranty, and impact on schedule.
Total Value: The Ultimate Measure
A deep dive into total cost then leads us to the ultimate concept of “total value.” With a total value perspective, you can’t turn your back on the subtleties of variance, cycle time, wasted trips to the jobsite, in-process rework, or impact on overhead and administrative costs for the builder, suppliers, and trade contractors alike. You will even need to consider how inspection authorities will react to the new building methods and associated cost of time required to remedy their predictable concerns.
Don’t be surprised if, for some levels of application, zoning and planning authorities object to your new “factory-built” housing. A lot of baggage accompanies that term going back to the post-WWII era, some deserved, some not. And what about the local inspectors? The great majority have never seen homes built with the methods employed in advanced off-site manufacturing. For some inspectors, green tags will come easy. With others, you’ll be seeing red for a long time. It seems each week one of our TrueNorth field consultants reports on a case where a local inspection authority forced a builder to do something completely unnecessary, code be damned. Not long ago, I saw 2x12 headers sandwiched with OSB over closet doors bearing no weight whatsoever. The builder knew it was pure waste, but he had no luck shifting the local inspector’s point of view.
Will you have to train them? Are they willing to be trained? The point is: Don’t plow ahead with off-site strategies without first considering all of the factors and quantifying them as best you can. There’s simply too much at stake to risk an uninformed or underinformed decision.
Last month I laid out a preliminary structure for understanding bid price, total cost, and total value of on-site versus off-site methods, then using that model to make a legitimate comparison. The key elements are presented below.
On-Site vs. Off-Site Factors
- Design
- Direct labor and material
- Indirect labor and material
- Schedule/cycle time
- Site waste
- Overhead and admin
- Planned trips
- Wasted trips
- VPO (EPO/FPO/variance)
- In-process rework
- Warranty
- Equipment
Note that the order and descriptions have changed and evolved somewhat from the previous article, based on input from practitioners in the field and my own further thought. In theory, at least, off-site methods should result in cost reductions in each of these categories, except in No. 12 (Equipment) and perhaps in No. 1 (Design). Will these cost reductions prove out? Will a comprehensive measurement system reveal significant, margin-enhancing savings from the adoption of off-site manufacturing methods? That’s for each of you to determine, and we’re working on an Excel template to help you with that task. We’ll make the free template available to anyone after we’ve beta-tested it with 10 or 12 builders. (If you’d like to be part of the beta test group, send me an email.)
Similar to TrueNorth’s “Saved Day” and “Trip-Cost” calculators, which identify the true value of a schedule day and the true total cost of a wasted trip to a jobsite, respectively, by a trade or supplier, this “On-Site vs. Off-site Calculator” will benefit a huge number of builders. As with those other Excel templates, we only ask that you share what you learn.
Creating such a template isn’t a simple undertaking. The more you push for accuracy and capturing every possible nuance, the more complex the algorithm becomes and hence the instructions begin to resemble a tax form. It’s a delicate balance, and we’re still accepting input.
Halfway through the process though, I had to back up a stage. The best first step is to consider the different types of off-site manufacturing, which have myriad combinations and permutations. Here’s how it looks at this juncture, although this, too, will no doubt evolve: eight levels of complexity, starting with the most complex listed first, down to the simplest at the end.
1. Fully modular is the most complex to produce off-site but is the simplest to assemble on-site. The interior and exterior walls and roof are fully framed, essential mechanicals are in place, and finishes range from partial to virtually complete. On-site cycle time drops to an absolute minimum, with nearly zero waste and the smallest possible need for on-site labor.
2. Off-site assembly with on-site erection involves open-frame interior and exterior walls, roofs, and various components built off-site, trucked in, then placed with a crane by captive crews. Major cycle-time savings result, with remarkable precision in construction, efficient engineering designed-in, significant site labor reductions, and minimal waste on site.
3. Precut and labeled frame packages see lumber packages precut and precisely labeled off-site, like a Lego set with a coding number on every single block. Engineering and utilization of material improves and the pitfalls of “making it up as you go” are eliminated, as is nearly all lumber waste on site. Some framers will deny it, but cycle time should drop.
4. Conventional combinations—any mix of the more well-known factory-built components listed below. Each element added increases the complexity of the comparison calculation but reduces complexity of the build—a more than fair trade-off.
5. Roof trusses reduce on-site labor, on-site waste, and cycle time, but large or high trusses may require the expense of a crane to set. With few exceptions, trusses are standard in most states from the Mid-Atlantic to the Midwest, North, and West, while stick-built roofs still hold a large share in southern states including Texas and the Southern Plains.
6. Wall panels reduce site labor, on-site waste, and cycle time, while more sophisticated panels, such as SIPs (structural insulated panels), may eliminate additional trade labor and simplify purchasing. Large or second-story panels may require the expense of a crane to set. Improved engineering and more efficient use of materials are cited in theory, but our observation in the field finds this is often not the case. Employed to varying degrees across the country, cycling up and down over the past 70 years, the expected dominance of wall panels hasn’t come to fruition.
7. Engineered/precast foundations are typically “modularized” basement wall panels formed off-site, trucked in, and placed by crane on footers poured on-site, resulting in significant improvement in precision of dimensions, quality, water resistance, and cycle time. Cure-time is virtually eliminated.
8. Subcomponents. Anything built off-site that can be delivered ready to install. There are myriad applications here, from simple pre-hung doors to prebuilt stairs, cabinets, stoops, compressor pads, etc. Labor and site-waste savings as well as cycle-time reduction are part of the equation.
Remember: Total Cost and Total Value Are What Matter
Of course, you’ll find many combinations of the above, such as off-site trusses and panels placed by traditional framers on-site on a pre-cast foundation, but this gives us a solid place to start. Once you establish your level of on-site vs. off-site for comparison, keep reminding yourself to confront the home building obstacle that just won’t go away: procurement of labor and material by bid-price alone. There’s no viable argument for buying on bid-price alone, except to save purchasing managers’ jobs because their bosses just don’t get it. That’s a lousy excuse, but I have great empathy for purchasing staff working with this scenario. It may sound harsh, but buying on anything else but true, total cost with an understanding of total value is either stupid or willfully ignorant.
Can we really create a universal template that will work for all possible scenarios? I believe we can get very close, but in each case, you’ll need some final massaging of the numbers based on local conditions and circumstances. I’m confident that 30 years from now—perhaps 20—those who follow us in home building will look back at today’s construction methods and wonder, “What were they thinking?”
I sent a pre-publication version of Part 1 of this column out to a number of folks who are applying off-site methods or have done so in the past. The feedback was interesting and adds much to the discussion. Using the same process with this column, I’ll collect more advice, warnings, encouragement, and admonitions. Your feedback is both welcome and needed.
Meanwhile, for those of you holding back, waiting until off-site methods prove out, that’s completely understandable. You’re not losing profit or market share—yet. For those who are experimenting with new approaches and leading the way, you have our thanks and admiration. You’re boldly going where no builder has gone before. Maybe this time we’ll go all of the way.
For a free PDF of Scott’s columns examining on-site vs. off-site construction and links to TrueNorth’s Excel templates, email your request to [email protected].
About the Author
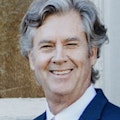
Scott Sedam
Scott Sedam is president of TrueNorth Development, a consulting and training firm that works with builders to improve products, process, and profits. A senior contributing editor to Pro Builder, Scott writes about all aspects of the home building business and won the 2015 Jesse H. Neal Award, business journalism's most prestigious prize, for his commentary in Pro Builder. Scott invites you to join TrueNorth's Lean Building Group on LinkedIn and welcomes your feedback at [email protected] or 248.446.1275.