This article has been updated since its original publication date of Dec. 12, 2005
While traditional solid sawn lumber remains a popular choice for home builders primarily due to their familiarity with the product and because its costs can be initially lower, engineered lumber is continuing to gain popularity, driven in part by rising lumber prices, which are also spurring introduction of new technologies that use more wood species and utilize small-dimension wood and wood residues to make composite structural panels and engineered wood components.
According to the U.S. Department of Agriculture, market share for engineered wood products such as glulam, I-joists, and laminated veneer lumber (LVL) is forecast to continue its steady growth, with glulam production during 2017 (271.3 million board feet) up 5.6 percent from the previous year; engineered wood I-joist production (518 million linear feet in 2017) up 7.5 percent from the previous year; and LVL (laminated veneer lumber) production (73 million cubic feet in 2017) up by 12.3 percent from a year earlier.
Other factors affecting the choice of dimensional lumber vs. engineered wood products include:
- Product quality issues with dimensional lumber, which can become costly for builders to correct after installation
- Dimensional lumber's limits: smaller depths and lengths because its size is dependent on the size of the timber cut to make it.
Major players in developing and manufacturing engineered wood products for the home building industry include: Boise Cascade, Georgia Pacific, Huber Engineered Woods, LP, Universal Forest Products, and Weyerhaeuser.
Key Terms for Engineered Wood
Engineered wood, also known as composite wood, consists of a range of wood products that are made by joining veneers, fibers, strands, and particles of wood with adhesives to form man-made composites. This category of building materials includes a variety of products ranging from plywood to joists to roof trusses.
Prefabricated Wood I-Joists
Prefabricated wood I-joists are structural, load-bearing products. I-joists are typically available in long lengths and because they're lightweight, have the advantage of being easily handled at the jobsite without the need for costly handling equipment. Their "I" configuration provides high bending strength and stiffness characteristics.
That "I" configuration consists of an upper and lower horizontal component—flange—and a vertical section—web—between the flanges. Flanges are made from laminated veneer lumber or laminated structural lumber and range in size from 1 5/16 to 1 1/2 inches thick and from 1 1/2 inches to 3 1/2 inches wide. The web is typically made of OSB (oriented strand board) and is either 3/8 inch or 7/16 inch thick, depending on its application in a residential installation.
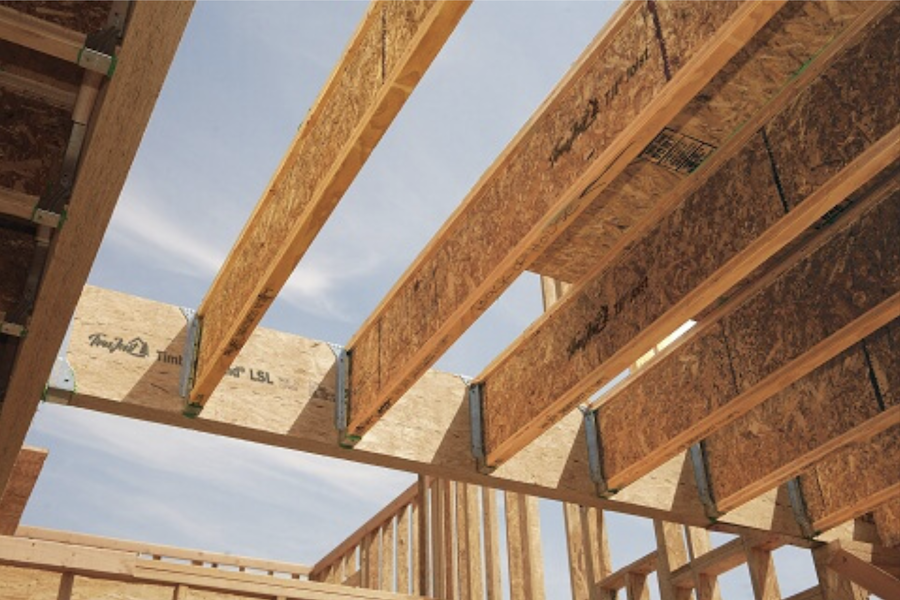
I-joist depth can also vary. Depths from 9 1/2 to 16 inches are common in residential installations, while depths of up to 48 inches are possible for commercial applications.
RELATED
- Engineered wood market forecasts
- Efficient framing practices
- 5 common framing errors and how to avoid them
- APA's advantages of advanced framing
Glued Laminated Timber (Glulam)
Glue laminated timber (glulam) is an engineered stress-rated product created by bonding together individual pieces of lumber having a thickness of 2 inches (50 mm) or less. Individual pieces of lumber are end-joined together to create long lengths referred to as laminations. These laminations are then face-bonded together to create the finished product. A little more than one-half of U.S. glulam goes to new residential construction and remodeling uses.
Species of timber, type of glue, and preservative type and application are all factors in glulam's durability, but, correctly specified, glulam can offer a durable, low-maintenance solution. Advantages of glulam include:
- Suited to long-span and curved designs, glulam offers strength without compromising design intent or aesthetics
- Timber has an excellent strength-to-weight ratio compared with steel or concrete, and glulam offers about 1 1/2 to two times the strength-to-weight ratio of steel of the same load-bearing capacity. One advantage of reduced structural weight is that the building's foundation can be smaller.
- Glulam engineered wood beams have low moisture content (about 12 percent at production stage). For regular green lumber and kiln-dried lumber, moisture content is, respectively, about 20 percent to 50 percent, and 12 percent. As a result, glulam can absorb moisture from the surrounding air without cracking, making it a suitable choice for more humid climates.
- It offers high strength and dimensional stability. Where solid timber posts and beams will crack and twist, glulam members will remain stable.
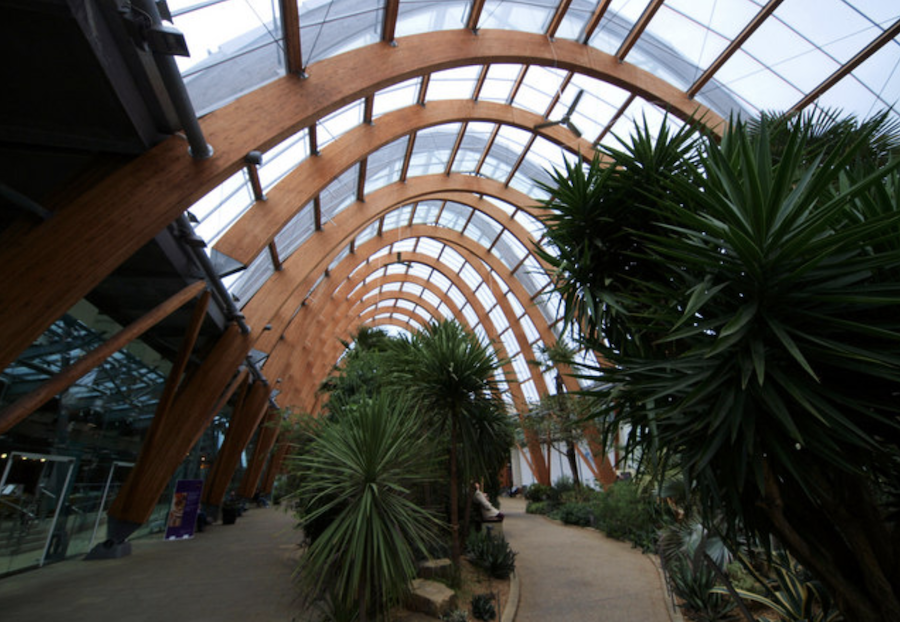
Laminated Veneer Lumber (LVL)
Laminated veneer lumber is produced by bonding thin wood veneers together in a large billet so the grain of all veneers is parallel to the long direction. Advantages of LVL include:
- The ability to use small logs to make large-dimension LVL products available in long lengths
- Uniform structural properties due to the material's thin-veneer layers being pre-graded for stiffness
- High strength due to LVL's low variability and randomized wood properties in thin layers
- The ability to cut and machined LVL using normal woodworking tools
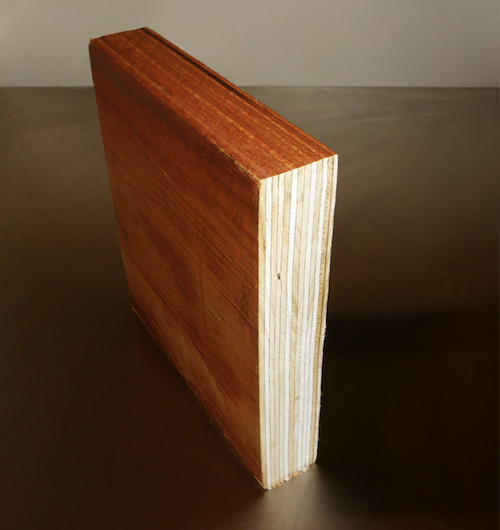
According to the APA — The Engineered Wood Association, North American production of most engineered lumber products is forecast to rise significantly over the next five years. The growth of engineered wood products is testimony to the technological adaptability of the wood products industry in the face of a changing wood fiber resource base.
"With less traditional and public forest timber available for wood product manufacturing, producers have had to improve existing methods and invent new ways to make more with less, and with alternative wood fiber resources," Jack Merry, communications director at the APA — The Engineered Wood Association. "The industry is responding with marked success to that challenge."
Engineered wood example: Modern Barn House Using Weyerhaeuser Trus Joist Parallam PSL
Although the term engineered lumber is used to describe a variety of materials, most are defined as structural components that have been fabricated. Engineered wood is manufactured by bonding together wood strands, veneers, lumber or other forms of wood fiber to produce a larger and integral composite unit that is stronger and stiffer than the sum of its parts.
Probably the most significant contributor to the increased use of engineered wood is the total installed costs are less than that of dimensional lumber. Additional benefits are related to ease of installation, dimensional stability, and structural integrity of engineered products. "Engineered wood products actually improve upon many of the inherent structural advantages of wood," adds Merry. "Cross-laminated plywood and oriented strand board, for example, distribute loads along-the-grain strength of wood in both panel axes. Glulam beams and wood I-joists can carry greater loads over longer spans than is possible with solid sawn wood of the same size," adds Merry.
An Engineered Solution Offers Advantages
Consistency of the material quality is the key advantage of engineered wood. Fabricated from dry materials to very tight manufacturing standards, engineered wood I-joists generally do not shrink, warp, cup, crown, or twist. Quality assurance programs are required during manufacturing to ensure the final product is of uniform strength and stiffness. These factors all contribute to the product's dimensional stability.
The manufacturing processes required for wood products add costs, making engineered lumber more expensive per linear foot than traditional sawn lumber. "The benefit is realized in total installed cost of the product," according to Mike O'Day, manager of engineered lumber for Georgia Pacific. "The installed costs consist of material usage, and labor requirements for installation. Engineered lumber can speed installation time and reduce labor since they are lighter and can be spaced further apart than dimensional lumber. The result is typically a lower total installed cost per square foot with an engineered product," adds O'Day. Engineered wood also reduces the number of callbacks for builders. Squeaky, or bouncy floors are usually expensive to correct. Installations using engineered wood I-beams can significantly reduce callbacks related to this problem.
Manufactured wood products are also environmentally friendly. "With the advent of forest farming as a primary source of wood fiber in the U.S., it is getting exceedingly difficult to find a resource that will permit the milling of larger pieces of framing lumber. [Engineered] wood I-joists can be manufactured in depths exceeding 48 inches and lengths over 40 feet and use up to 60 percent less wood fiber than solid-sawn joists. On the jobsite there is little or no waste," adds Edward L. Keith, P.E., senior engineer for the APA — The Engineered Wood Association.

In addition to the common nominal 10 and 12 inch depths, engineered wood I-joists are made in depths beyond that of traditional framing lumber. Depths up to 48 inches and lengths limited only by ground transportation and handling are available to builders. An advantage over lumber is that a deeper I-joist member is only incrementally more expensive than a shallower member because it is made deeper by adding more web material. Ordering I-joists cut to the exact length required means 100 percent utilization in the field, resulting in little or no waste on the jobsite.
Because of their "I" cross sectional shape, engineered wood joists weigh up to 60 percent less than lumber joists, making engineered wood components easier to handle. The flange permits a firm, comfortable, secure grip even when the joist is wet or covered with wood dust. A single worker can easily handle a joist up to 25 to 40 feet in length.
Strength Characteristics of I-Joists Relative to Conventional Wood Framing
With respect to conventional wood framing (16 inches or 19.2 inches on center wood joist spacing), I-joists are 50 percent stiffer than solid sawn lumber. In terms of strength, for simple spans, an I-joist series with the lowest design values (PRI-20) can span to within inches of the strongest solid sawn lumber joist (S. pine). In multiple span situations, I-joists have an advantage because solid sawn lumber in lengths greater than 20 feet is quite rare and expensive. Building dealers and I-joist manufacturers have substitution analysis software and can provide this service free of charge in most cases.
Limitations of Engineered Lumber
Like traditional lumber, engineered wood does have its limitations. The key to understanding acceptable applications is in education of the materials. Currently, most engineered wood products are limited to interior use.
Lack of familiarity with the product: Resistance to specifying engineered wood generally comes from subcontractors that are not familiar with the product. Subs need to be careful when installing plumbing and electrical that must be routed through engineered wood. Careful consideration needs to be taken where and how it is cut. "Holes less than 1.5 inches diameter are generally OK as long as they're not on or into the flange. Drilling through the web material is normally an acceptable practice," O'Day says.
Installation errors: Damage to wood I-joists within a structural system is normally associated with notching of the flanges or misapplication of the manufacturer's web hole information. Designing a repair for a damaged I-joist can be difficult and requires an understanding of I-joists and of adhesives and fasteners that may not be familiar to many designers. Fortunately, most manufacturers are more than willing to provide fixes for most applications. There are a number of products currently working through the code acceptance system that can be used in the field to restore the joist to its full capacity without having to have the solution engineered.
Fire safety concerns: Another concern centers around fire safety of engineered wood I-joists. From the fire service point of view, prefabricated wood I-joists, due to their "I" form with OSB web between the top and bottom flange, have a history of collapse hazards when exposed to fire. Underwriters Laboratories, in collaboration with the Chicago Fire Department, Michigan State University, and the International Association of Fire Chiefs, undertook a fire research study, which it published in 2006, aimed at understanding the hazards to firefighters posed by the use of lightweight construction in the form of wood trusses and engineered lumber in roof and floor designs.
Engineered Wood and Construction Industry Trends
Installations using engineered wood products have increased over the last 10 years. And, according to Allied Market Research, the engineered wood market is forecast to grow at a compound annual growth rate (CAGR) of 24.8% from 2016 to 2022, reaching over $40 billion by 2022.
The growing popularity of engineered wood products can be attributed to a range of factors, including:
- Fluctuating dimensional lumber supplies and prices
- Education of home builders about engineered wood materials and their advantages
- Introduction of green building standards in several U.S. states, such as Washington and California, which in turn encourages development of more engineered wood products linked with low emission levels
- Increasing consumer acceptance of engineered wood products.
Advertisement
Related Stories
Awards
6th Annual Most Valuable Product Awards
Drumroll ... Please join us in celebrating our 6th Annual MVP Awards winners, which represent the best in innovative building products
Sustainability
Fortera Takes Concrete Steps to Reduce the Climate Impact of Cement
Clean-tech company Fortera, which uses technology to capture carbon emissions form cement manufacturing, will open its first commercial-scale operation on April 12, 2024, in California
Building Materials
Lumber Leads Building Materials Prices Higher in March
Overall, the cost of building materials rose during March, with softwood lumber, gypsum products, and concrete all seeing price increases. Only steel mill materials saw price drops